PRINTING
Textile label printing
Custom textile label printing solutions
For over 25 years, Louison Industries has distinguished itself as an expert in industrial textile printing. Specializing in a wide range of printing technologies, we offer high-quality, innovative and customized finishes that enable our customers to stand out on all media, whether paper or textile.
Textile label printing is at the heart of our expertise. We integrate state-of-the-art printing technologies into our manufacturing process, enabling the creation of textile labels that are both functional and attractive. Whether you need labels for garments, fashion items, industrial products or other specific applications, we offer tailor-made solutions for every need.
We use a variety of printing technologies to meet the diverse requirements of our customers: offset, digital, thermal, screen and flexographic printing. Each method brings its own specific advantages in terms of print quality, personalization, resistance and production speed.
As specialists in textile label printing, quality and safety are our top priorities. Our textile labels are produced to rigorous industry standards, guaranteeing excellence and durability. We have Oeko-Tex certification, which testifies to our commitment to products that are environmentally friendly and free from harmful substances.
Offset printing
Offset printing is characterized by the repulsion/impregnation effect of ink on a paper substrate. The idea is to spread ink over a surface with dry and wet areas. The process is based on the use of plates to transfer an image onto a blanket cylinder (also known as an offset cylinder), which is then printed onto paper. This inexpensive printing technique is generally used in the communications (catalogs, brochures) and press sectors, not least because of its high print-run capacity.
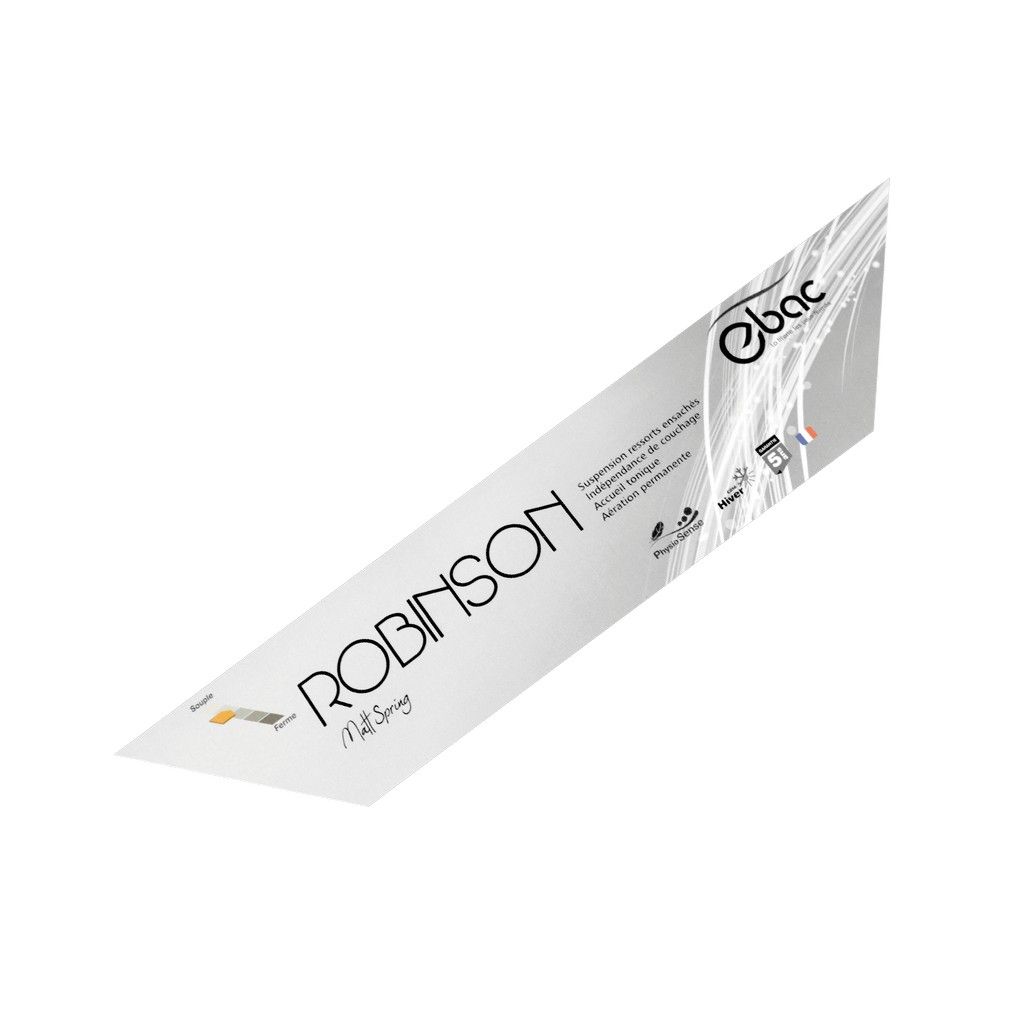
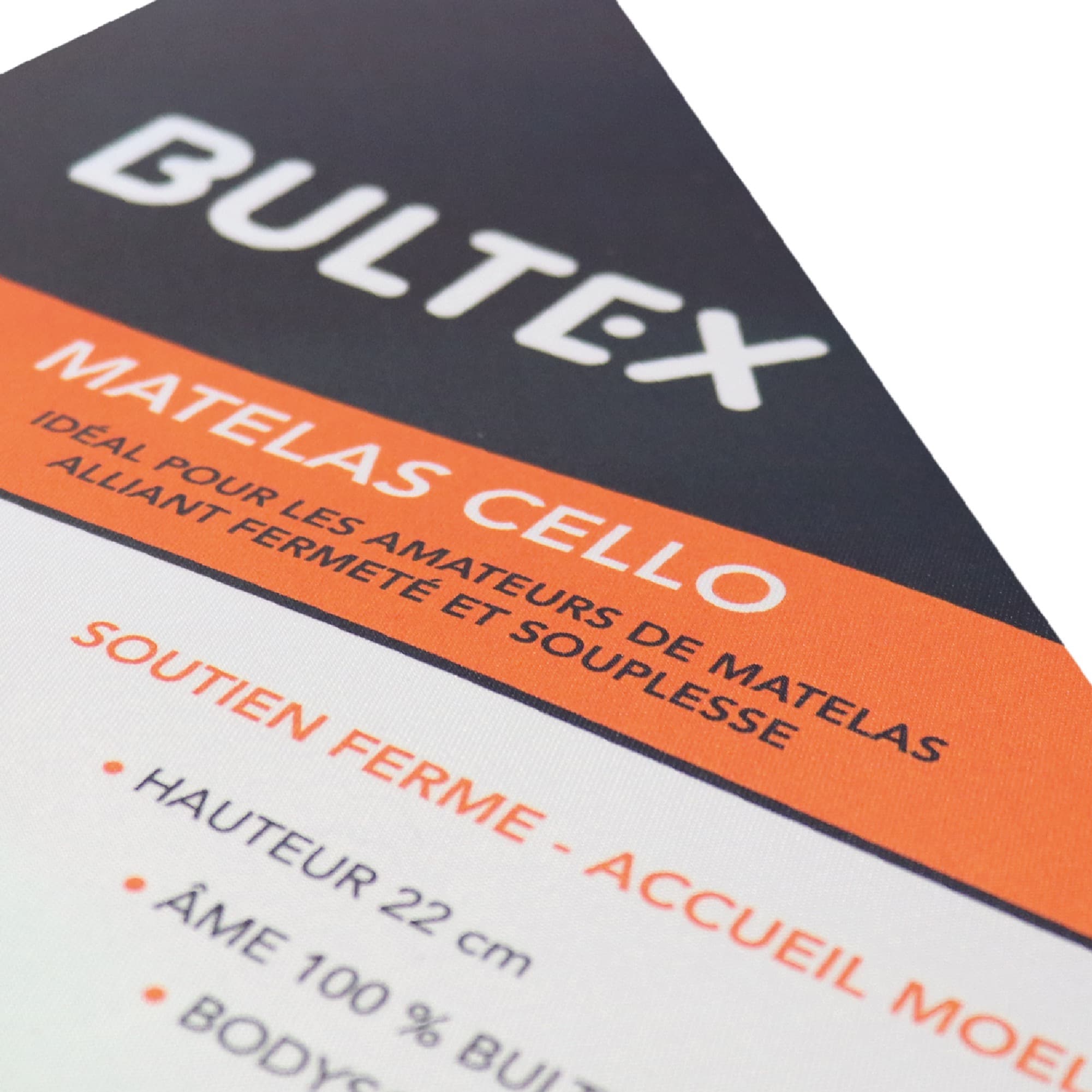
Digital printing
Digital printing is characterized by the total absence of preliminary steps, giving it a speed advantage over other printing styles, for high quality rendering on both small and large formats. Digital printing involves printing onto paper from a data set. Unlike offset printing, which is designed for a large number of print runs, this technique can be used to produce small or medium-sized print runs as required.
Thermal
Fast and reliable, the thermal printer uses heat to print results on special paper. The distinguishing feature of this printing process is the total absence of ink. The paper passes between the thermal head and the roller feeding it. The heat creates a reaction between the paper and the pigments to generate text and images.
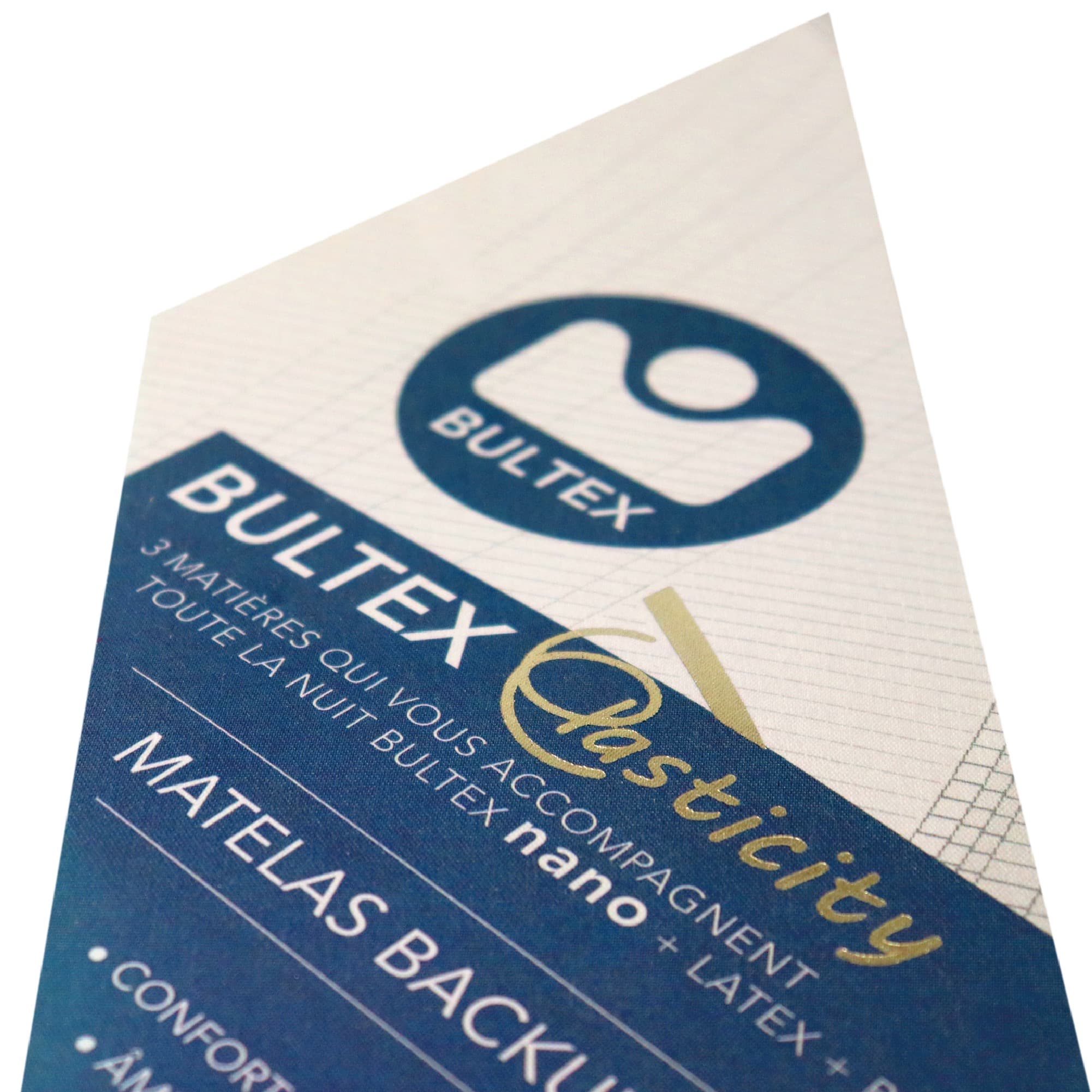
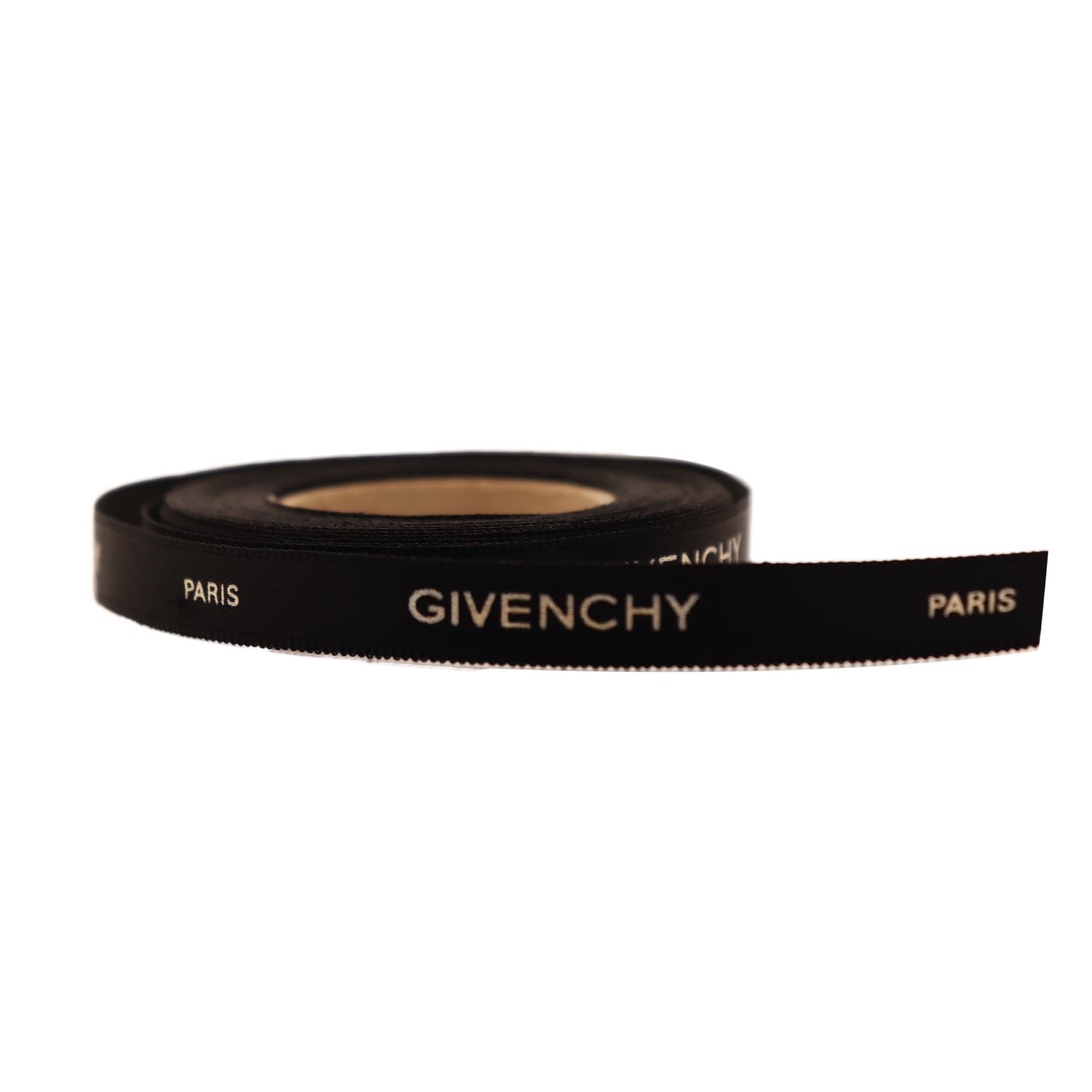
Screen printing
Screen printing is a stencil printing process. This technique stands out for its incredible colorfastness and the highly detailed rendering of graphics on textile substrates. The stencil consists of four elements: a screen printing frame, a photographic emulsion, a light source and a graphic model printed entirely in black on an insulating film. The ink is then squeegeed through a screen and deposited on the textile. Screen printing offers numerous advantages. In addition to its colorfastness and detail rendering, it’s an inexpensive technique that can be used to print large surfaces in large runs.
Flexography
Flexography is a relief printing process similar to letterpress. The printing form (clichés or sleeves) is made of photopolymer. This process is used to print corrugated cardboard, plastic bags, labels, etc. It’s a fast-growing printing process, thanks to its low cost and eco-friendliness. In fact, thanks to the use of fluid inks, this direct printing principle enables high-speed
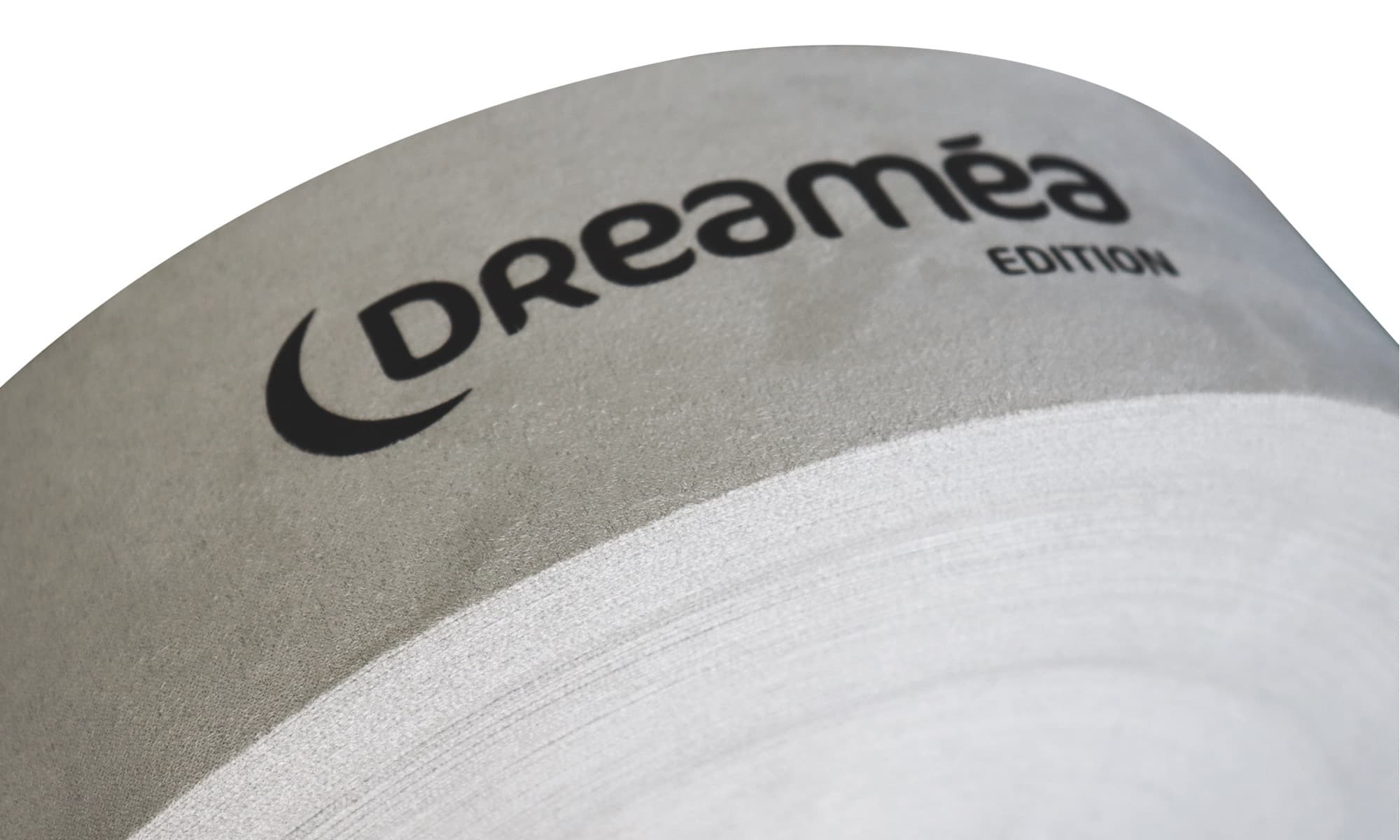
OUR APPROACH
Consulting, research and manufacturing
Our innovative approach allows us to accompany you as a true partner, from the project idea to the industrialization of the finished product.
Consulting
Our large experience in the world of textiles and plastics processes enables us to advise and guide you in your choice of products. If you encounter technical problems with one of your textile or plastic products, we are here to find solutions. Tell us about your projects so that we can help you solve your problems. We are no longer just your supplier, we become your partner!
R & D
Basic and experimental research is in the company's DNA. We are always on the lookout for new technologies from our suppliers and partners, so that we can offer you the most innovative solutions on the market. Our 2 laboratories allow us to carry out all kinds of research, development and tests quickly in order to develop and perfect new manufacturing processes and new materials.
Manufacturing
We are able to design products from existing models or we can create a new product based on your specifications or a jointly developed specification. We study the constraints linked to the realization of your product, and we propose the most economical solution that meets your needs. If we can integrate a large part of eco-responsibility from the design stage, we will do so with passion.
FAQ | Textile label printing
What methods are commonly used for printing on ribbons and textile formats?
Commonly used methods for printing on textile ribbons and formats include screen printing, digital printing, sublimation, flexography and thermal transfer printing. Each method offers its own advantages in terms of print quality, speed and cost.
What types of fabric can be used for printing on ribbons and textile formats?
A wide range of fabrics can be used for ribbon printing and textile formats. This includes natural fabrics such as cotton, linen and silk, as well as synthetic fabrics such as polyester, nylon and rayon. Some fabrics require special pre-treatment for best printing results.
What are the most important features to bear in mind when printing on textile ribbons and formats?
When printing on textile ribbons and formats, it's important to consider aspects such as washfastness, color stability, sharpness of detail, flexibility, lightfastness and the adhesion of the ink or dye to the fabric. These characteristics vary according to the printing method and materials used.
What equipment is required for printing on textile ribbons and formats?
The equipment required for printing on textile ribbons and formats depends on the printing method chosen. They may include a special textile printer, a printing table, inks or dyes adapted to the type of fabric, drying systems, thermal fixing equipment and finishing devices.
What are the advantages of printing on textile ribbons and formats?
Printing on textile ribbons and formats offers many advantages. It allows for personalization and the creation of unique designs, offers a wide variety of colors and patterns, enables fine and intricate details to be printed, can be produced in small or large quantities, and offers good durability and resistance to washing.
A project ?
Contact us
With LOUISON INDUSTRIES, benefit from more than 140 years of know-how and experience in the field of textiles and plastics processes.